碳中和背景下平齿机节能改造的三大技术路径
在"双碳"目标驱动下,传统机械加工设备亟需通过技术革新实现能效提升。平齿机作为齿轮加工领域的设备,其节能改造可从以下三大技术路径展开:
一、电机与变频驱动系统升级
采用永磁同步电机替代传统异步电机,结合矢量变频控制技术,可提升动力系统能效15%-25%。通过实时采集负载数据,变频器可动态调整主轴转速与扭矩输出,避免空载或轻载时的无效能耗。某企业实测数据显示,改造后单台设备年节电量达8000kWh以上。配套能量回馈装置可将制动能量转化为电能回馈电网,进一步降低综合能耗。
二、工艺参数优化与冷却润滑革新
基于数字孪生技术建立加工过程模型,通过AI算法优化切削参数组合(如进给量、主轴转速),在保证加工质量前提下降低15%-30%的切削能耗。采用微量润滑(MQL)技术替代传统浇注式冷却,压缩空气与微量润滑油的喷射可减少90%的冷却液消耗。结合陶瓷涂层刀具等新型材料,实现干式/半干式切削,冷却液处理带来的环境负担。
三、智能化能源管理系统构建
部署工业物联网平台,集成电流、振动、温度等多维度传感器,实时监测设备能耗状态。通过边缘计算分析设备能效曲线,自动识别异常耗能工况并触发预警。建立能源管理数字孪生体,模拟不同生产排程下的能耗分布,为优化设备启停策略提供决策支持。某项目应用表明,系统级节能管理可使整体能耗降低12%-18%。
通过机电系统升级、工艺技术创新与数字化管控的深度融合,平齿机节能改造不仅能实现单机能耗下降30%-50%,更能推动齿轮制造向绿色低碳生产模式转型。未来需持续探索氢能驱动、余热回收等前沿技术,构建零碳加工新生态。
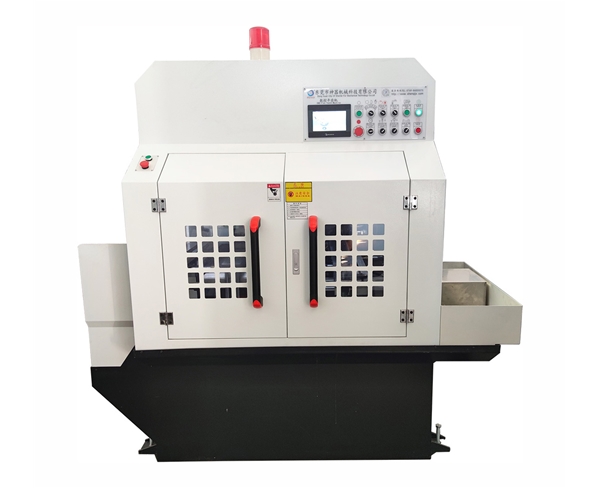
下一条:没有了